SEALING FEATURES IN RIGID PACKAGING
- Amita Jain
- Sep 10, 2020
- 4 min read
Updated: Sep 10, 2020
While designing rigid packaging, it is necessary to add adequate sealing features on the closure of the packaging for a longer shelf life of the product. It is very important to understand which kind of sealing feature should be provided for products to sustain a longer shelf life. For designers and engineers, they need to add this as a critical design requirement while designing and developing any rigid packaging.
Disclaimer: All the definitions are mellowed down and have my own version to explain how things workaround. This has not been taken from any website or dictionary.
What is sealing?
When the closure has surfaced to surface contact such that there is no-gap or micro millimeter of a gap for air or liquid to pass outside, hence making it leak proof. The sealing is designed in such a way that it avoids outer gas and atmosphere to react with the inner substance thus increasing the shelf life of the product inside. It does not accelerate any heat or cold temperature conditions but keeps the product intact by not reacting with the outside temperature or gas.
Generally, there is only one definition of sealing but as I worked closely with engineers I understood there are two types of sealings that we should provide in our packaging. The two types of sealing which are critical to design and engineer for rigid packaging are:
1. Factory sealing: This sealing is done during manufacturing. This sealing is designed in such a way that the product inside the packaging does not leak or react with outside temperature from the time it is dispatched from the factory to retail, till the consumer opens the package. Once the consumer opens the package the seal might not be that effective. Hence, there is an additional need for operational sealing features for daily use.
There are different type of sealing in this category:
Pressure seals(wad seals/freshness seals)
Induction sealing
Foam cap liners

2. Operational/Repetitive Sealing: This sealing is designed for everyday use. Here once the factory sealing is removed. This helps to avoid moisture to enter the packaging hence, avoids degrading of product. Operational seals are not as effective as factory seals but act as moisture resistant.
Here few seals work as repetitive seals
Interference seal: Plug seal is used for a lot of shampoo bottles where filptop cap is used. It is also used for factory sealing as it is quite effective.
Pressure fit seals: where it is fit through friction for example cork in a glass bottle
There is always a confusion that the tamper-proofing feature can also act as a sealant and can prevent leakage. There are few tamper-proof features that help in tight closures and prevent liquids to come out but they not act as a sealing feature. For example, there can be confusion that shrink sleeve is used for sealing but it just provides tamper evidence and barrier properties.
Tamper proofing: A tamper-resistant package is one having an indicator or barrier to entry which, if breached or missing, can be reasonably be expected to provide visible evidence to the consumer that tampering has occurred.
Let's dissect a few packaging and understand how these three features - factory seal, operational and tamper evidence work hand in hand.
I have taken three different SKUs of a different quantity to understand what's the difference in each.

5L Oil can
1L oil bottle
200ml bottle
1. 5L Oil can

It's a 5L oil can
CTC Fliptop cap
It has overflow control fangs inside to help users to pour easily into another container with the control
Sealing: It has an interference sealing where the surface is contacting the surface in pressurized condition hence making the packaging airtight
Tamper proof: The bottle has a pull tab tear as tamper evidence. The user can easily tear the membrane for accessing the opening. The interesting part is the pull tab membrane passively helps in sealing the bottle.
2. 1L Oil Bottle
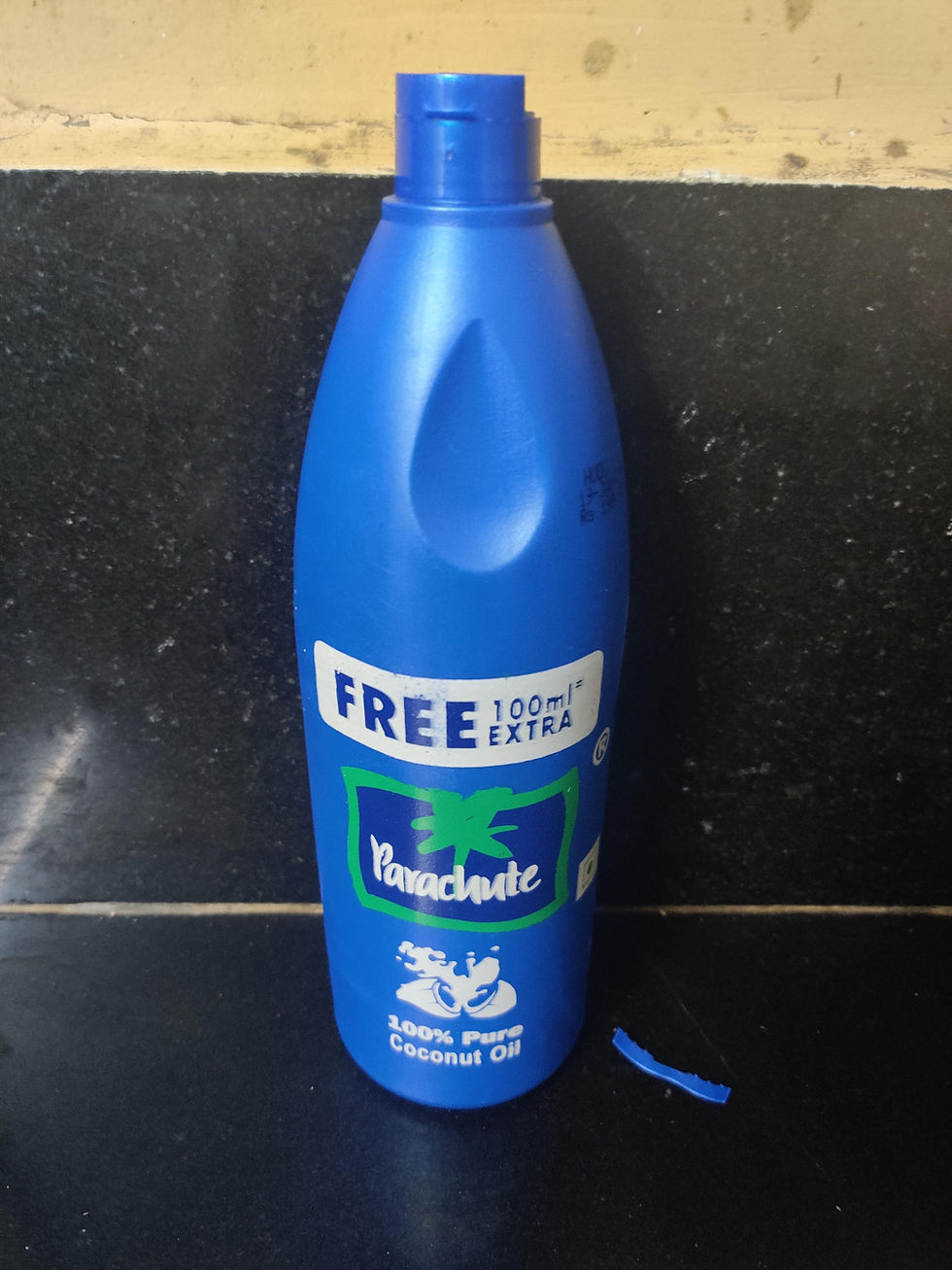
Minimalistic bottle with flip-top cap
Plug seal
Tamper evidence
Sealing: It has a plug seal that seals the bottle operationally. Plug seal is inserted into the reamed passageway after the tapered pin is flushed with the plug there is controlled expansion that causes the lands and grooves on the O.D. of the plug to "bite" into the surrounding material, forming a reliable, leak-tight seal for both liquids and gases.
Tamper Proof: There is a tear band feature to pull and open. Very intuitive and easy to open. We have might have seen this in multiple packaging like talcum powder, food jars, etc.
3. 200ml Syrup Bottle
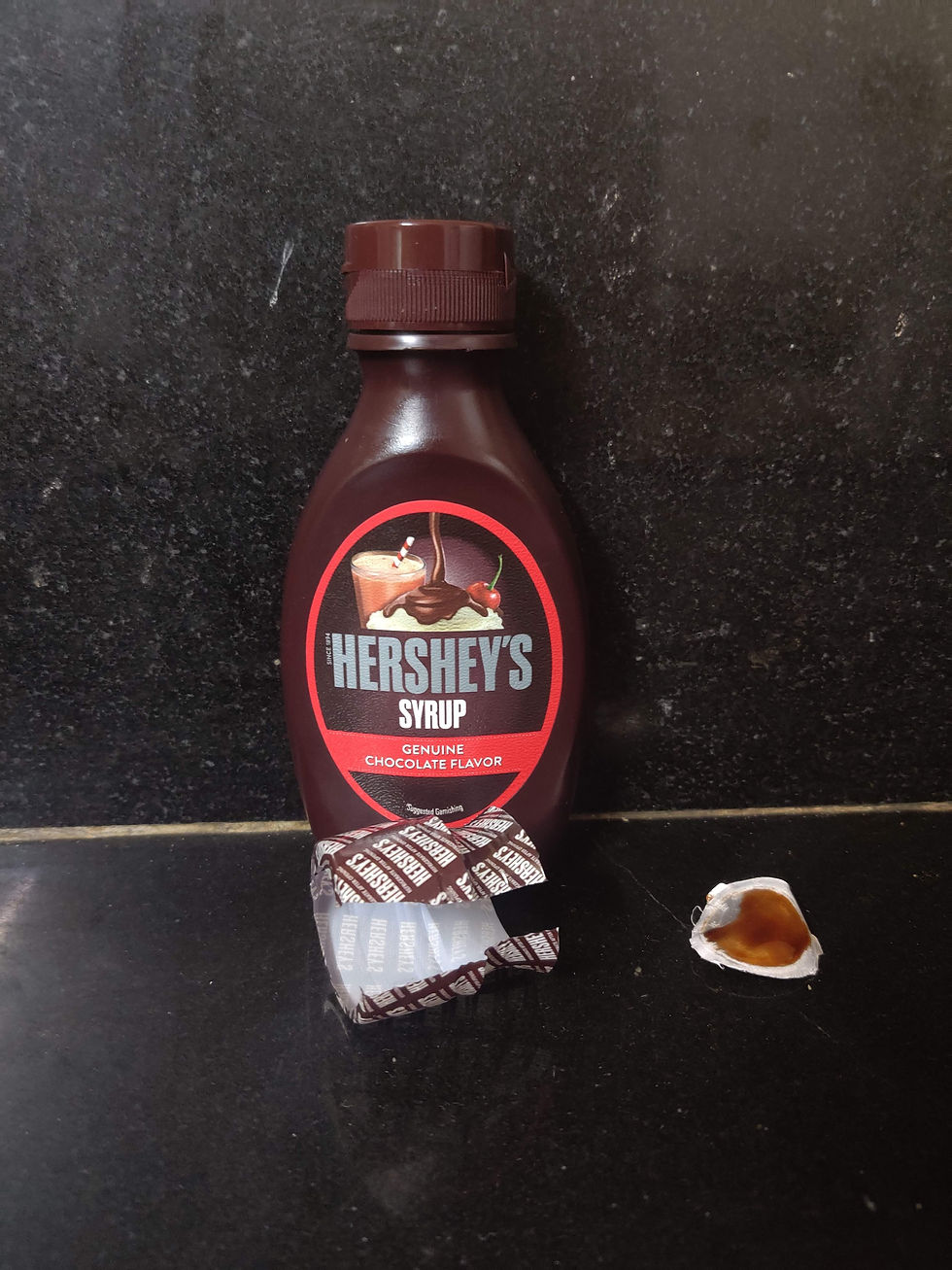
It has two types of sealing: Factory and operational
Shrinkwrap for tamper evidence and for providing a better barrier property
Wad seal is for Factory sealing and tamer proof
Plug seal for repetitive sealing
Sealing: There are two types of sealing provided
An induction seal/freshness seal is used to close the neck closure. It also acts as tamper evidence
Plug seal is used for repetitive use. As you can see in the image below.
Tamper Proofing: Heat Shrink sleeve is used for tamper-proofing and also acts as a barrier. It has a great advantage as it also provides a good branding space.
As we start dissecting more products we will start getting into the technicality of each feature and how we can use this as inspiration while developing new packaging.
I hope this might have resolved some confusion if you had any and for the people who are investing in new product development do keep these features in mind while getting your packaging designed.
If you have any product packaging and want to discuss these critical features, feel free to catch up with me at amitajain16@gmail.com
-Amita
Comments